Keeping your crews safe and working in the Summer should not be hard or expensive but there are things you can do that will make a difference in them wanting and being able to do the work you need them to do the entire summer.
First have your equipment working in tip top shape and that includes the A/C in your trucks. Although it is not good for workers to experience a large temp shift going in and out of a vehicle while working (from the Sahara to the Arctic), having the A/C set at a reasonable temp, 10 degrees cooler than the outside temp, with a large volume of air moving does help.
Have plenty of water available while at work. Large plastic water coolers, like Igloos
are a good investment for your employees. Every worker should have there own water bottle that they can fill from the cooler. Remember they should be consuming at least 8-12 oz of water per hour while working outside.
Tip: Save on the cost of buying ice; clean and use 1/2 gal or quart size (juice or milk) bottles filled with water that you freeze over night in your work freezer (or at home). You can fit 3-4 of these at the bottom of the cooler before filling it each day and the ice bottles will slowly melt and even when the cooler is empty the melted bottles can be poured out and used them selves. Have extras and each morning when you take the frozen ones out put new ones in and they will be ready for the next morning.
Make sure everyone has and wears a hat and UV sun glasses. Wide brims are better then baseball caps but anything helps. If your uniform or employees own shirts are short sleeved ask them to use sun screen. Long pants and water proof shoes are best to work in but can be hot. Suggest light cotton instead of jeans for pants and suggest thin moisture wicking socks instead of the heavy cotton which will trap sweat and become even heavier. Heat escapes the most from the head and feet, keeping the feet hot can really make you feel worse. Materials should be light weight but tight weaved or come with UV protection in the fabric if possible.
Believe it or not but Dollar Stores like the chain "Dollar Tree" can be both you and your employees best friend. They carry many things for summer. You or your employees can spend around $5 per person and be set for all day in the sun.
Things you can get for $1:
Neck bands that you can soak in cold water that contain water gel beads that expand and then retain the cold that you tie around the neck. These are a Great value. I use these myself when working outside or down at hunt camp and they are great.
Sun Screen Sticks UV rated 30-50 in packs of 2-4 (depends on the store) great for the face, ears and neck. They also carry sun screen in liquid and sprays.
UV lip balm, because almost 70% of lip cancer is from the sun, not tobacco products.
UV Sun Glasses, even ones that wrap around, to stop eye sun exposure. May not be the most fashionable and supplies vary but at least worth a look, plus not a big loss when they are lost or break. Be sure to check that they are UV, some of them are not.
Water bottles. They have all types, plastic and metal, and in all sizes, shop around to find what you like. Some even have belt clips or loops. 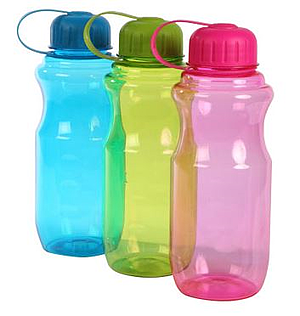
Fine mist spray bottles. Keeping a spray bottle with cold water in it that employees can mist on themselves will help keep body temps down, fend off heat stroke and allows evaporation from dampening clothing keeping them cooler.
Tip: these bottles can also be put in the freezer half filled with water so more water can be added beginning of the day and lets the ice melt over time.
Hats or visors. They may not be a fashion statement but I have seen some nicer ones sometimes. Keep checking and when you find one you like buy 2-3.
Small hand fans or clip on fans. Even though you have to spend another $1 for batteries these little fans can help a lot when used while sitting in the shade on a break to cool you down.
Dollar Tree even has a web site where you can buy items direct by the case so you do not have to go looking for them. Check out http://www.dollartree.com products change all the time so check often.
If you want to spend a little more money, then head to a Wal-mart or similar and buy the spray bottles with the built in fans. Those mist and blow air at the same time. 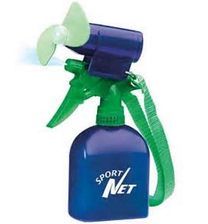
OSHA does not have set rules as to how much water you need to supply, just that you do. They do not require employers to supply clothes, sun screen, UV sun glasses or other sun protection items but anything you want and can give your employees will make them feel like a well thought of and valuable member of your business.
But Please follow OSHA guidelines they do suggest https://www.osha.gov/Publications/OSHA3166/osha3166.html
and OSHA also has a new Summer campaign "Water. Rest. Shade." that you can read about here; https://www.osha.gov/SLTC/heatillness/heat_index/work_rest_schedules.html
Have a great rest of your Summer and stay safe.